Stanley Electric Co., Ltd., a leading Japanese manufacturer of automotive lighting and electronic components, has been a pioneer in leveraging innovative technologies to enhance its operations. The company’s journey from grappling with operational inefficiencies to achieving streamlined production through IoT monitoring is a testament to the transformative power of digital solutions.
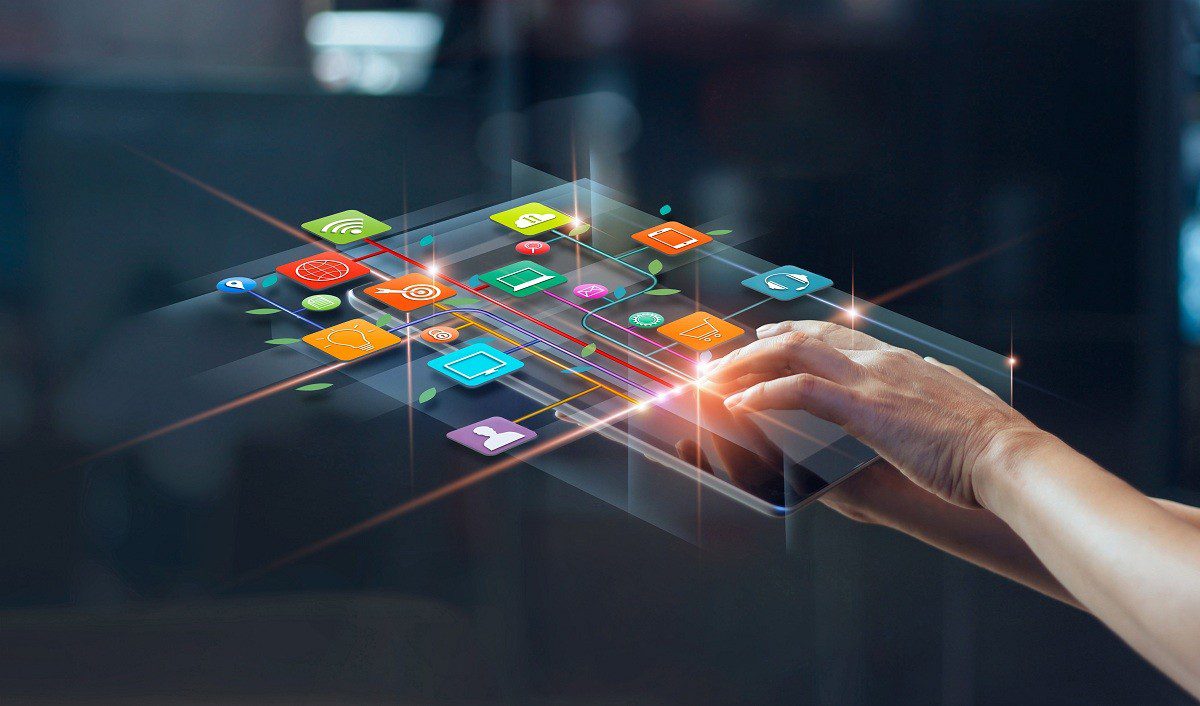
Adopting IoT Monitoring Systems
The Challenge: Managing Complex Global Operations
As a global corporation with 23 factories across eight countries and over 16,000 employees, Stanley Electric faced significant challenges:
- Inefficient production workflows: Lack of real-time visibility into manufacturing processes led to delays.
- High defect rates: Quality control issues in automotive lighting products, a core business area, impacted customer satisfaction.
- Rising operational costs: Inefficiencies in resource allocation and inventory management increased expenses.
These obstacles hindered the company’s ability to meet growing demand from major clients like Honda, Nissan, Toyota, and Ford.
The Solution: Adopting IoT Monitoring Systems
To address these challenges, Stanley Electric implemented an IoT monitoring system across its key production facilities. This system included:
- Real-time tracking of production data: Sensors installed on manufacturing equipment provided instant updates on performance metrics.
- Predictive maintenance capabilities: IoT-enabled analytics helped identify potential equipment failures before they occurred.
- Integrated dashboards: Centralized platforms allowed managers to monitor operations remotely and make data-driven decisions.
By creating a connected ecosystem, Stanley Electric optimized its manufacturing processes and improved collaboration across departments.
The Results: Measurable Improvements
The adoption of IoT monitoring yielded impressive results for Stanley Electric. Key metrics include:
- 20% reduction in production downtime:Real-time alerts enabled swift responses to equipment issues.
- 15% improvement in product quality: Enhanced oversight reduced defect rates in automotive lighting systems.
- 10% decrease in operational costs: Streamlined workflows and better inventory management minimized waste.
- Increased client satisfaction: Faster delivery times and higher-quality products strengthened relationships with major automotive brands.
Client Testimonials
Ông Takanori Kitano, President of Stanley Electric, praised the impact of IoT on the company’s operations:, Chủ tịch Stanley Electric, nhận định:
"The integration of IoT monitoring has transformed our manufacturing processes. We are now more agile and efficient, which allows us to better serve our clients worldwide."
A senior manager at one of Stanley’s factories added:
"With real-time data at our fingertips, we’ve been able to proactively address issues before they escalate. This has been a game-changer for our team."
Next Steps
Building on this success, Stanley Electric plans to expand its IoT initiatives across all 23 factories globally. The company is also exploring advanced AI-driven analytics to further enhance predictive maintenance and operational efficiency.
Interested in Transforming Your Operations?
Learn more about how IoT solutions can revolutionize your business. Contact us today to explore tailored strategies for your industry!